The Slab
This building would have been a lot easier from almost every angle if it was not
for the design of the slab. This 4" piece of concrete which provides a solid floor
for the building is reinforced with a metal mesh to which long tubes of cross-
linked polyethelyne (PEX) are attached. The theory is that hot water will be pumped
through these tubes and the heat will be sucked out by the concrete which will
then apply the heat to my feet as I shuffle around the place barefoot in midwinter.
The problem is that if you just plop down a concrete slab on the prairie floor, it's
more than likely that during the winter and the spring, the ground will heave up and
down and your floor will crack like a New England road. If there is $1000 worth of PEX
in the floor, it will be torn apart until it fractures. If there is hot water being
pumped through the tubes, well, you're fucked. This is why there is a 4' deep frost
wall around the perimeter of the building instead of 22 4' deep holes with poles
sticking out of them.
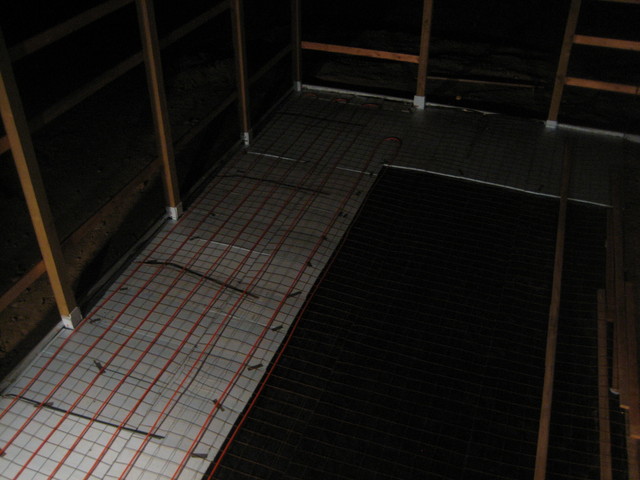
We started by laying down a 6 mil sheet of black plastic which acts as a vapor barrier,
keeping our concrete from soaking up water from the ground, and keeping the ground from
pulling all of the moisture out of the concrete as it sets up. Over the plastic, we
unrolled possibly the most ungainly object I've ever touched: a big, rusty roll of
6" wire mesh. We pressed the Rrebar that was sticking out of the frostwall into a 90
degree angle and wired it to the mesh. Then we spent a long time unrolling the second
most ungainly object I've ever touched: a 1000' roll of PEX. We initially purchased a
bunch of 200' rolls, but the day before we started unrolling, Chris realized that putting
several hundred feet of PEX with joints inside fiber concrete was pretty much asking
for trouble. I get enough trouble that I don't ask for, so we picked up the orange roll
and the rest will go back to Lowe's.
One of the tricks with the PEX is that you don't want to have a run over 300' because the
circulating pumps will have trouble moving that much water. Another issue is that when you
break up your floor into 300' runs, you want to make sure they are all equal lengths, since
runs of unequal length will get different amounts of water due to the difference in flow
resistance, and your floor will have cool and hot spots. The challenge: cover the entire
floor with runs of equal, unknown lengths of tube while only cutting the 1000' roll 3
times. Ready, go.
And it went rather smoothly, except when we were done, we realized that the ground plus
the plastic plus the wire plus the tubes (plus the foam, which we put down around the edge
of the slab so that when it heats up, it will not bleed energy into the freezing ground
outside of the building) left us with about 2" in which to pour concrete. Not good. Since
it was about 10:30 PM by that point, a lot of whack ideas were put forward, but we ended up
just nailing a 2x4" in the 1.5" direction on top of the forms. This board will later be
removed and the second splash plank put in place.
The next morning, Lafarge showed up with concrete at 7:45 AM, 5 yards of it. The truck
parked outside the garage door and out came my favorite concrete truck driver. We chatted
for a bit about the best way to do this...
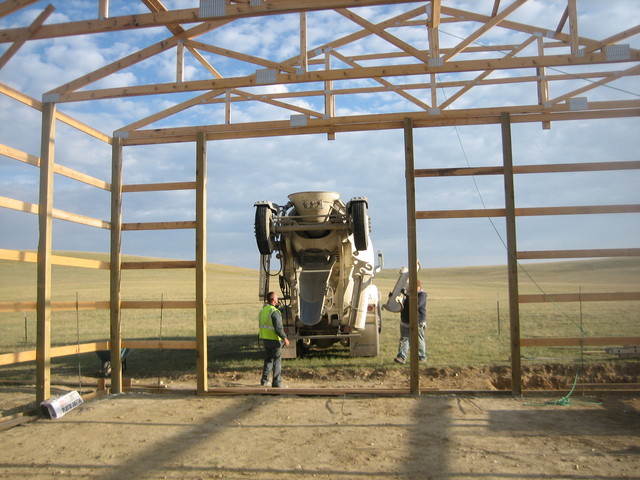
...and decided that the truck would probably have to come inside the building to get the
concrete into the other side of the building.
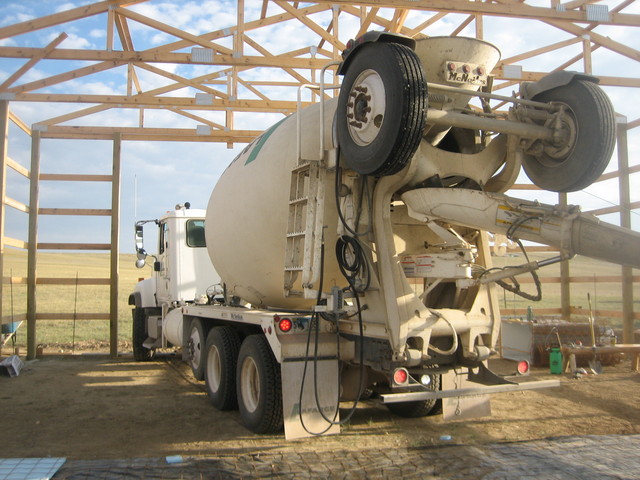
This place looked a lot bigger until we parked a Lafarge truck inside it.
The truck expelled 5 yards of concrete:
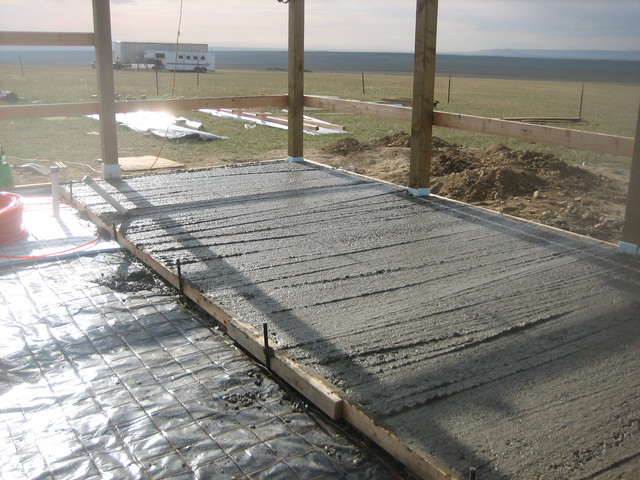
We, of course, needed about 6.
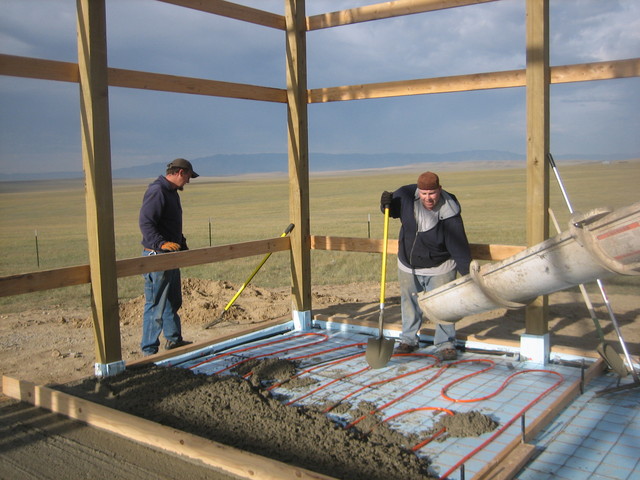
Best Readymix Operator On Earth called back to base and they sent another yard out, and
changed our instructions for our afternoon pour to 6.5 yards. We were a little concerned
that the mostly-finished pour would set up before the rescue truck arrived, but we kept
the pour wet and it did okay. Had it had time to harden, we would have been SOL because
of the tiny fibers we asked Lafarge to add to the mix; these fibers make it pretty much
implausible to break up concrete and start over. In this case, concrete really does only
set up once. No mistakes allowed, unless you want to look at them for the next several
decades. Lafarge helped out by moving their truck out to us quickly.
When the pour was done it looked a lot more respectable.
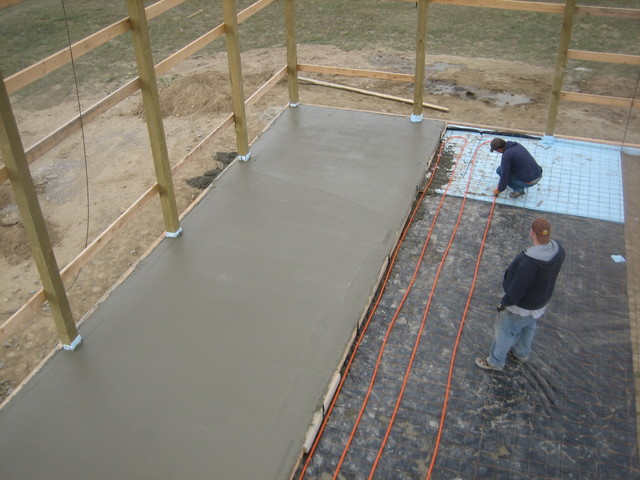
We started setting up for the second pour immediately. Our concrete, however, stopped
cooperating right around this time. We had planned initially to get the first truck and
the last truck out of the Lafarge facility on our Friday pour date, but we ended up only
being able to get a 7:45 AM truck and a 1:30 PM truck. This was barely enough time for the
first pour to set before the second pour. And set it would have to, because the first pour
acted as the south form for the second pour.
This put us in the uncomfortable and totally useless position of watching a bunch of concrete
drying waaaay too slowly, standing around screaming "dry you motherfucker or we are totally,
irretrivably hosed." The sun went behind clouds, the temperature dropped, the grey goo just
sat there and laughed at us. "Amateurs," it said. We ignored it and continued unrolling
our materials.
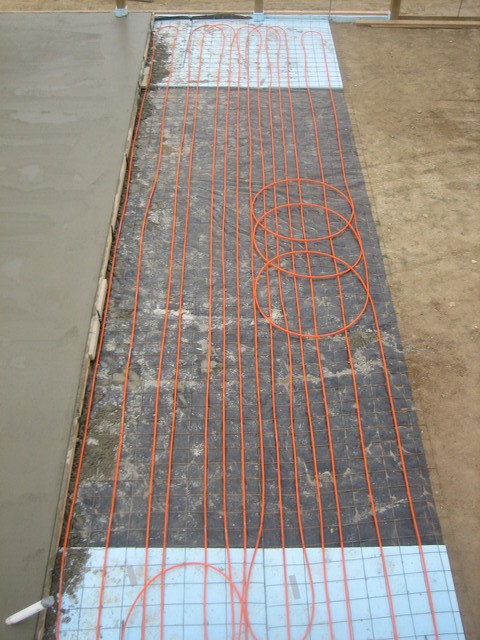
We popped the form off the first pour as the Lafage truck was showing up. I probably don't
need to mention that it was exactly on time, not even a minute late. But somehow the first
pour was dry, the form came off cleanly, and the concrete was hard enough to walk on by the
time we started pouring.
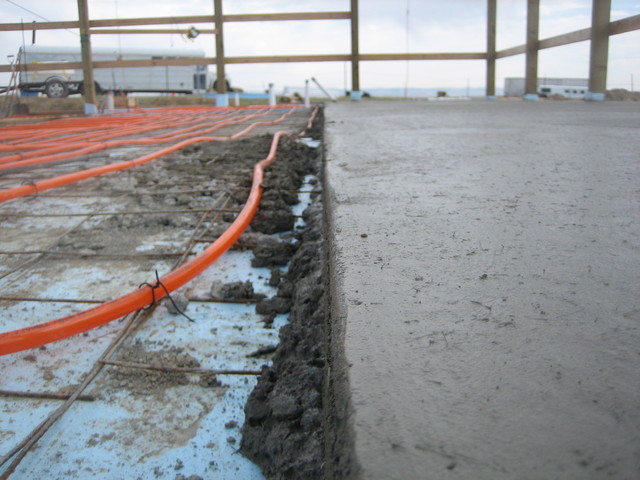
Concrete took a long time because it doesn't come on the weekends, and Chris was only able to
free himself from work on Fridays. After 4 Fridays of being ankle-deep in liquid rock, and
several emergencies that can only happen when you're dealing with concrete, we were left with
a floor and a good deal of sidewalk. I would advise the non-professional not tangle with large
amounts of flatwork, except that I'm sure it'd cost an arm and a leg to make contractors care
about the final finish as much as we did, and caring about the job really was the difference
on those days when it decided to blow a west wind at 55 MPH and whip dust across the floor, or
when the readymix operator decided to leave the PTO engaged when he tried to move the truck and
dumped half a yard on the ground 40 feet from where we needed it.
Final product:
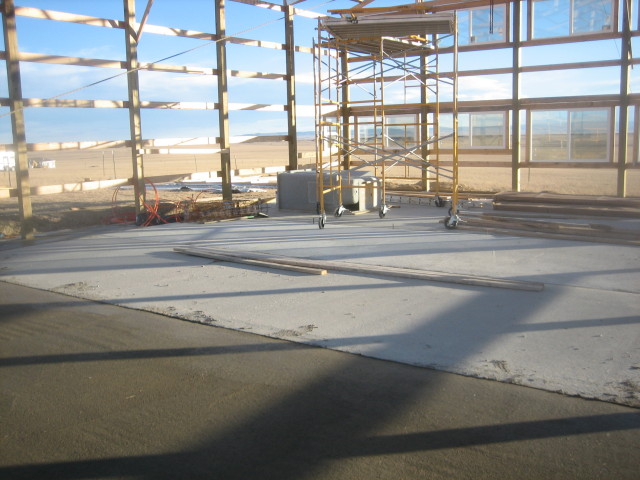
next