Roof
The experience of putting the metal skin on the walls of this building had me completely terrified at the prospect
of putting that same metal skin on the roof. For one, as August waned and we rolled into a Wyoming September, the
weather was getting steadily cooler and windier, and I couldn't see how our process of dragging these wild metal
sheets up behind us as we climbed ladders was going to translate to the roof. How would we rotate the sheets to
the plane of the roof without bending them over the eve at the top of the wall? And how would we hold down the
sheets before they blew away before we screwed them down? I was pretty freaked about this phase of the project.
My brother advised that is there was anyequipment that would make the job easier, I should get it. I wish I had been
given this advice sooner. We rented a total of three machines; the workhorse was a Genie scissorlift:
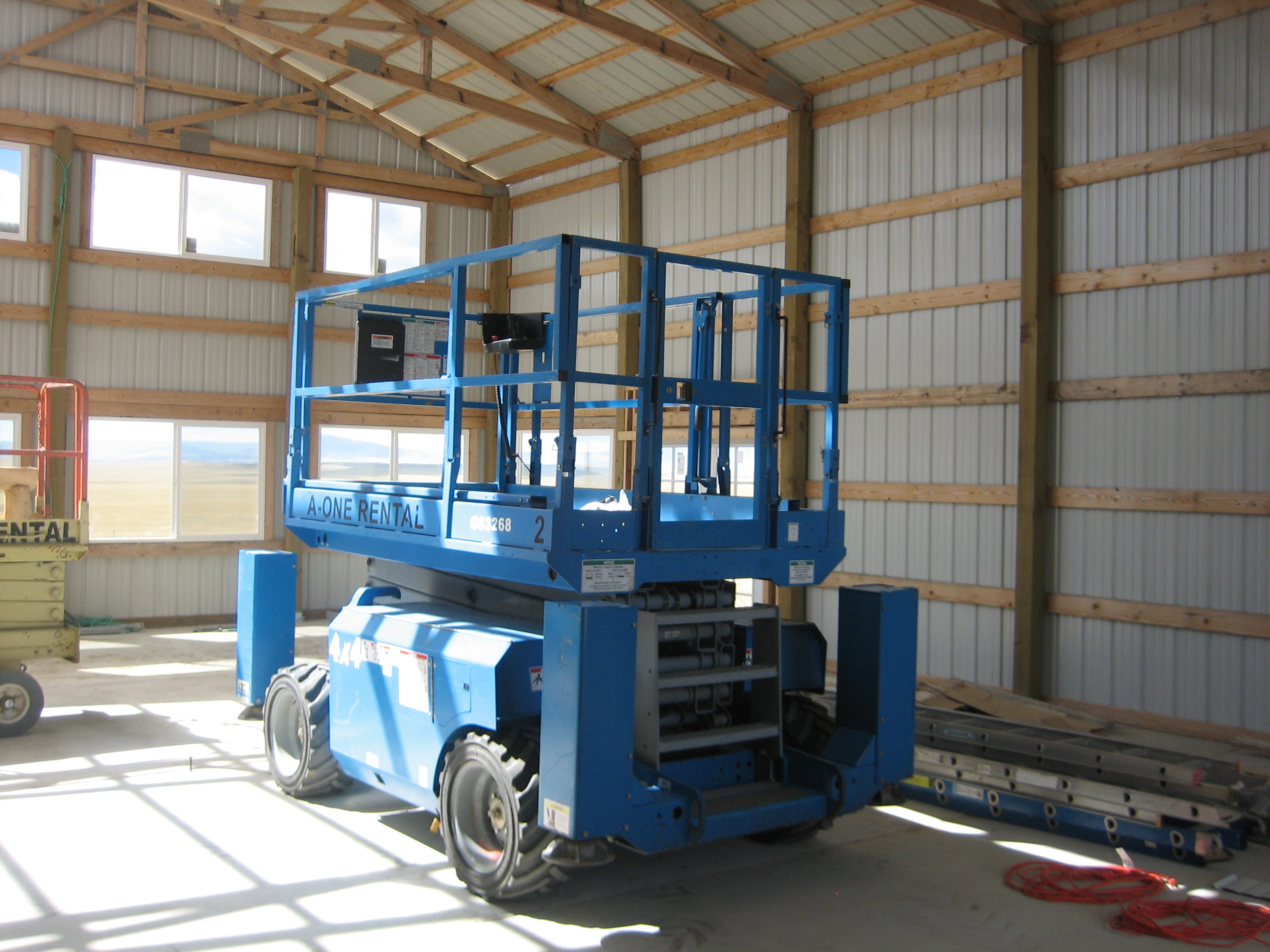
This thing was mega. It extends straight up to put your feet at 30 feet, which is a full 8 feet above the peal of
the roof of the building. To make this less terrifying, four hydraulic pistons act as outriggers, and best of all,
the outriggers are totally automatic, sensing when the machine is perfectly level. Brilliant. We also got hold of
an electric scissorlift that we could roll around the inside of the building, as well as a Genie Z-45 that you'll see
later.
The other thing we got for this task was way more human help. Chris enlisted Bob, Pat and Shane in addition to
Jerron. Jerron messed his foot up pretty bad in an unrelated off-road dirtbike accident (dirtbike totaled) and so
he was a bit hobbled but it really didn't slow him down. Shane is a professional metalworker; he does roofs like
this one all week long. Pat works at the place where Chris used to make custom furniture. He's rebuilding his old
family pickup from when he was a kid, soup to nuts, by hand. And you might remember Bob
from last fall when we installed the French door; he's from Wisconsin; he's Chris' main snowmobiling bud and he just
finished building a V-8 motorboat, by hand, from scratch, from plans he found on the Internet.
Basically, we're dealing with the A-Team of building things.
Chris and I went out on Friday night and my neighbor Mike brought his backhoe over to flatten out the piles of dirt
that had flattened out into ridges and bumps around the building. Mike is a semi-retired oilfield welder and he
is a magician with a backhoe; in about 30 minutes he completely formed the dirt around the building in the most
natural countour possible, leaving and easy track for the lifts to drive around the house. Mike is my first neighbor
with a backhoe and he is hereby allowed to borrow any of my stuff at any time, because that machine can save hours
of time and backbreaking work.
Chris and Jerron and Shane and I went out to the site early on Saturday morning and put up eave metal on the west
side and a row of 2x6"s along the top of each plane of the roof to attach the ridgecap later. Bob and Pat arrived around
10AM and we went to work on the metal sheets. We quickly adopted a process whereby Chris would apply silicone to the
inside of the trailing rib of the metal, then Chris and Jerron would pass the metal up to Pat and me in the Genie
scissorlift. We'd lay the metal down, parallel to the ground on the bucket on the scissorlift, and then we'd fly
up to the top of the roof; then we'd feed the sheet pu to Shane who was walkign on the roof, and Jerron who was in
the bucket of the electric scissorlift inside. Shane and Jerron would pull the sheet up to the top and me,
Jerron and Shane would hold the sheet down as we screwed it in place. On sheets where it was necessary, Chris would
go up in the Z-45 and manage whatever task he needed from there, be it guiding the sheet or screwing down the ends where
the indoor scissorlift couldn't reach because of the building's wall.
And it was that simple; I planned to get 8 sheets on during that first day, 8 Sunday, and then 16 more the next weekend
to finish the roof in 2 weekends. We got 26 panels on during the first day, leaving 6 more to finish up on a relatively
leisurely Sunday. The difference: a huge set of professional, skilled hands. Jerron is super strong and tenacious,
I enjoy learning about this stuff, but for the first time Chris had another skilled metalworker and two other very
experienced constructors in Shane, Bob and Pat, and they've all worked together before. Another key difference:
using huge machines instead of ladders and muscles. Work smarter, not harder.
Unfortunately I did not bring my camera on Saturday. On Sunday, all that was left to record was the last roof panel
to go into place:
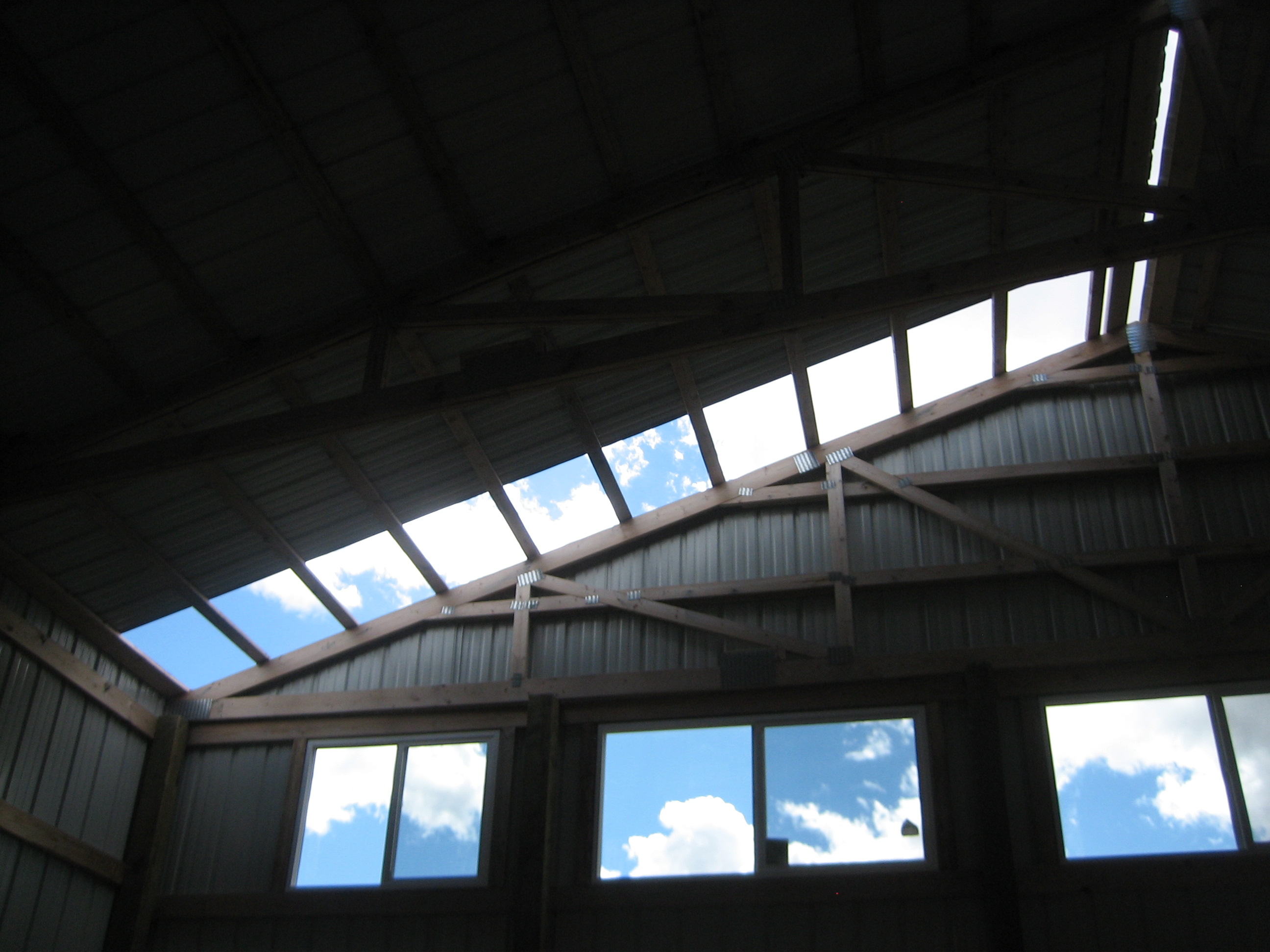
Sunday also saw Pat and Bob move onto other, somewhat less constructive tasks (copious alcohol + NFL). Shane and
Jerron spidered up on the roof while Chris and I worked on the Genie scissorlift bringing panels up to the roof.
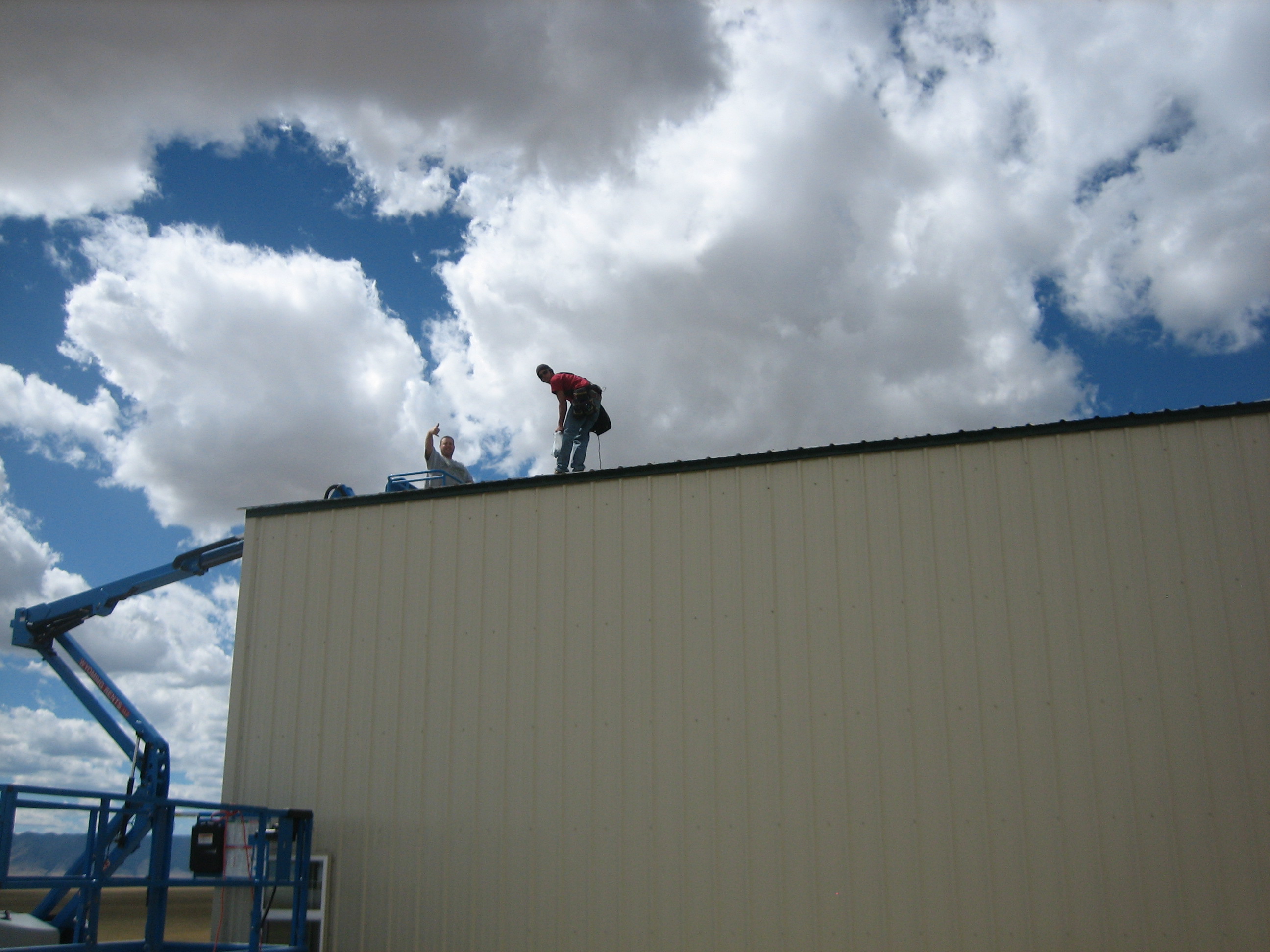
Every time I bugged Shane to put on a harness he drank a beer. Chris says a lot of people try to put safety first,
when really as long as you keep it in the top 5, you'll probably be okay.

The roof was finished in relatively short order. While putting on the ridgecap, Jerron commented that he thought
it was starting to rain, but within seconds it was clear that it wasnt rain falling from the sky, but thousands of
tiny flies or gnats. They stuck to wahtever they fell on, be it skin, clothing, hair, scissorlift, or the sides and
roof of the building. At first we retreated into the building and freaked completely out (hey, you'd freak out too
if you were doign a roof and suddenly a pestilence descended from the sky.) Then we manned up and went back up and
finished the ridgecap although I wore a garbage bag over my head so the bugs would stop crawling in my ears.
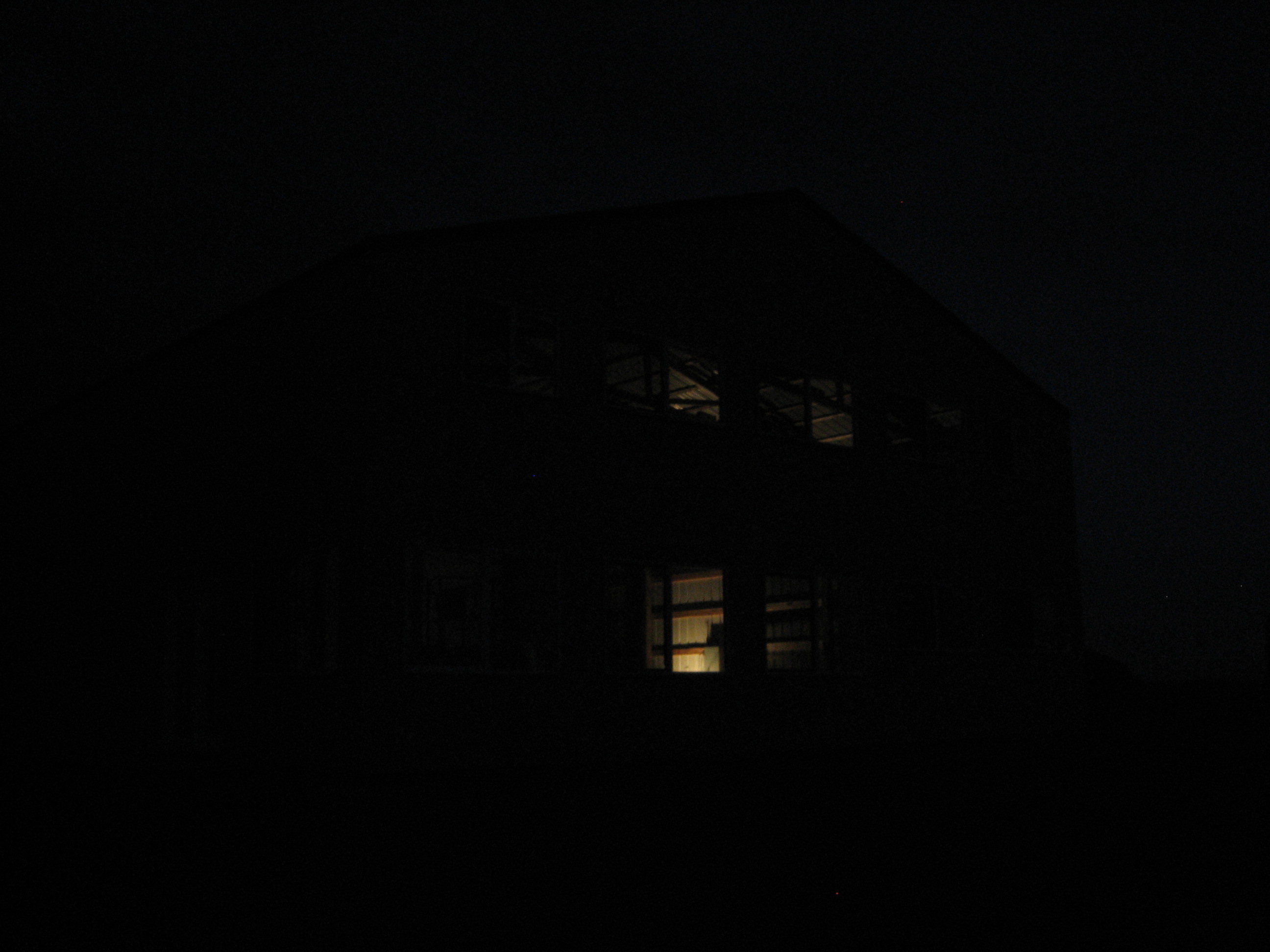
next