The Posts
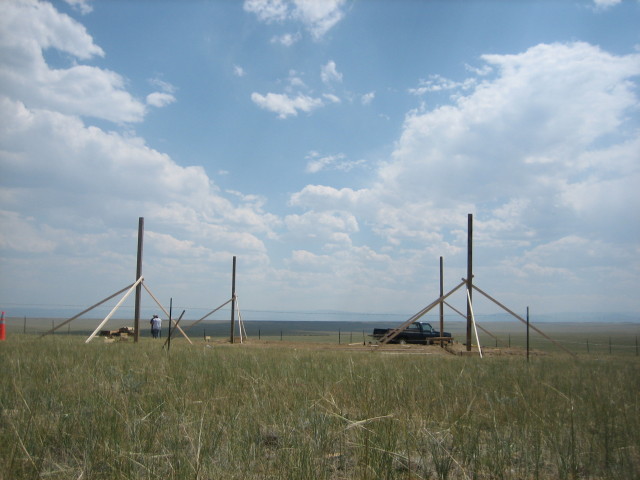
After the frostwall, we took a short break. I went to a wedding and when I
returned... the posts. The basic order for materials to complete the bulk
of the skeleton for the building was delivered by truck, and we got right on
the task of using up all the lumber. "The posts" in question are 20' and an
inch or so long, nominally 6"x6", although like all other American lumber,
actually a little smaller than that. And they were pressure treated, which
means that nasty chemicals are injected into the wood under pressure so that
they inhabit the outer inch or more of the post and inhibit even bugs from
munching on the posts.
The pressure treatment of these posts was undertaken by a true maniac who
decided if a little bit of the treatment was good, a lot is better. He's
probably right, bug-wise, but what he wasn't taking into account is that
I don't have a crane and therefore, my crew and I will be placing each
of 22 poles into position manually. Estimated weight of a pole: 225 million
pounds (800 kilometers). Why is treated wood so heavy? This is stupid, let's
return these and get cast iron beams, I tell Chris. Jerron picks up a beam on
his shoulder and starts running around.
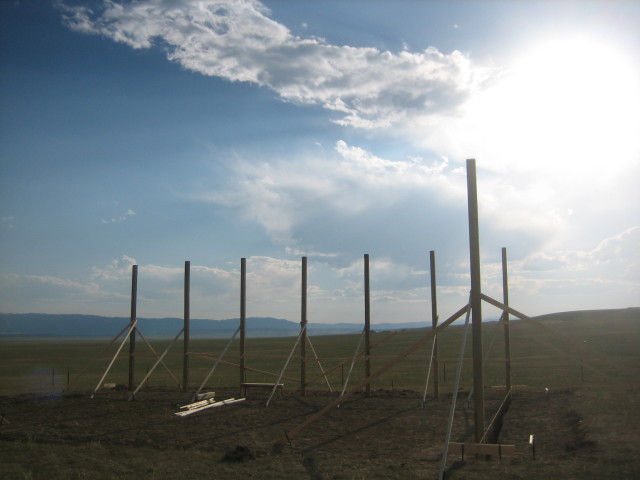
The posts take a damned long time to get into position: three full days and
nights of work. Chris uses the
ancient wisdom of Discovery Channel and runs the pole game like we're dealing
with obelisks; fulcrum beams went out over the trench and the posts were walked
hand over hand by Jerron into position and then whacked with a sledgehammer
for fine tuning. The only problem was that we needed to precisely align the
posts, but the trench was, well, not right where we needed it at all times.
So Chris fashioned up a "fake post", or a 6' long hollow rectangular prism that
was the standing for the real post when we were shaving the sides of the trench
in order to make the posts align with each other. This meant lots and lots of
digging dirt out of the trench, but luckily me and Chris picked up a bunch
of trenching shovels (really narrow head, long handle) which made the job suck
slightly less.
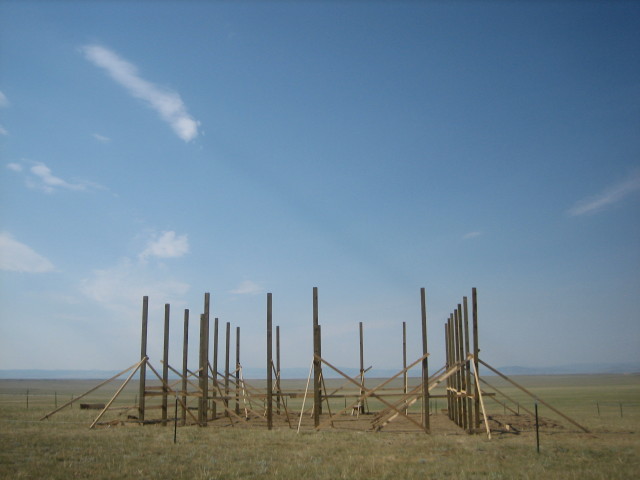
Posts were braced off with the material that we'll use to cover the trusses
lengthwise - 16' 2x4 perlins - nailed to the ground via 24" concrete spikes.
Girds
Once the posts were all braced off, we took a little break. I went to a
wedding in New Hampshire, and when I came back, Chris and I put up the bottom
two rows of girds, the horizontal 2x6s that link the posts together. We left
off girds where there would be windows or doors. This should have been easy
but when we were chalking the lines for the west side, I used a random nail
that was in the northwest corner post instead of waiting for Chris to take a
measurement. This meant that the girds on the west side slanted up about 24"
as they went north. Not cool. Everything on that side came off and we did it
again.
Also, around this time, the Coleman generator puked on us so we had to run this
whole game with a hand saw. Sweet!
next